Shock absorber, or damper, testing continues to grow in importance as electric and autonomous vehicle development drives a renewed focus on vehicle handling and ride comfort. MTS offers industry-proven solutions for a full spectrum of damper testing, including advanced capabilities for evolving EV/AV requirements.
Steven Kuplic - MTS Product Managerexplores the capabilities of Model 849 and 850 servo hydraulic damper test systems, which combine precision-engineered load frames and accessories, versatile controls and software, and state-of-the-art monitoring technologies to provide accurate, safe and efficient testing across a full spectrum of conventional and emerging applications.
Optimized over decades of real-world testing, MTS servo hydraulic damper test solutions deliver the dynamic, high-velocity loading required for advanced performance research or demanding, high-cycle durability testing.
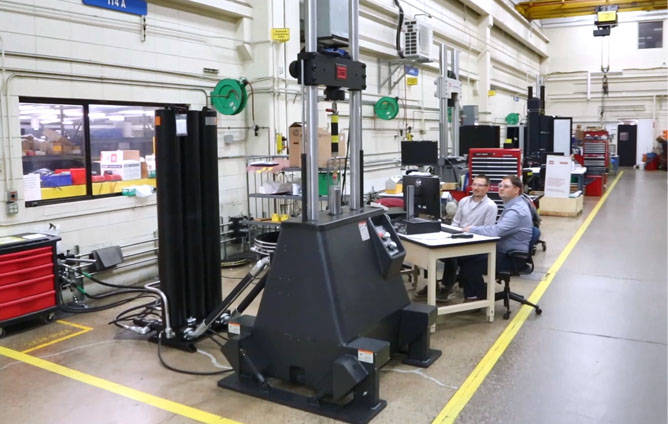
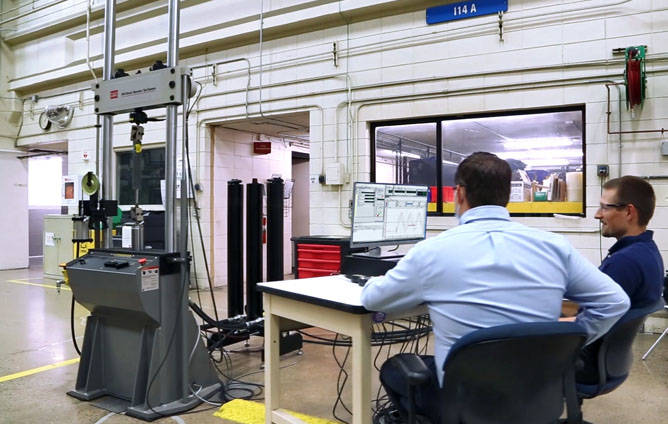
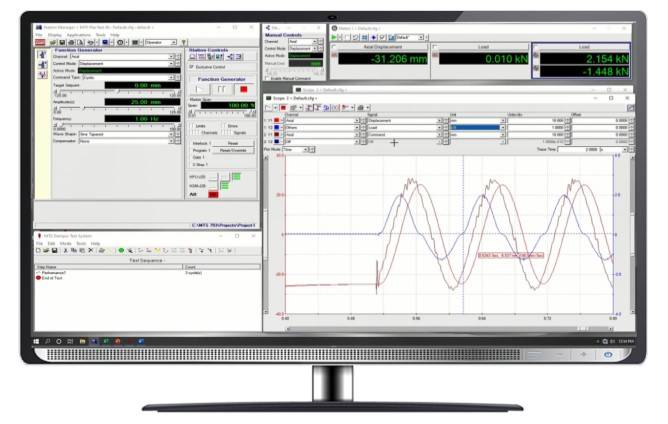
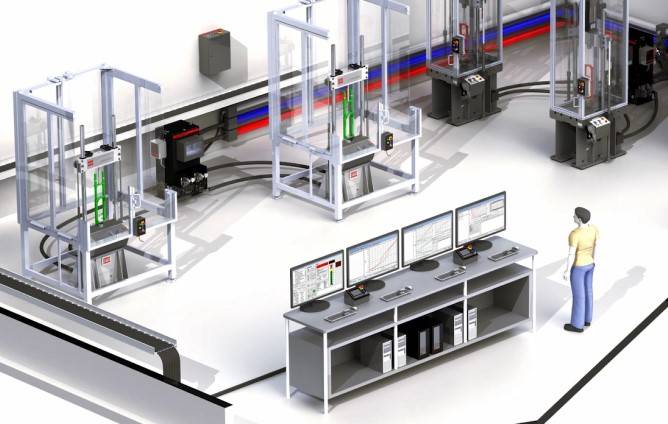