Hybrid Simulation: ImHIL Tire
The Iterative mechanical Hardware-in-the-Loop (mHIL) Tire solution combines a computational model with a physical tire test system and tire specimen to create a vehicle-level simulation environment that enables development engineers to investigate the interaction between tires and vehicles at the vehicle level.
Applications
Test Specimens
Key Product Features
Accelerated Testing
mHIL techniques compress vehicle development schedules by enabling meaningful evaluation and validation subsystems and vehicles earlier in development - well before the availability of vehicle prototypes
Innovative Technology
Real components can be substituted for difficult-to-model components when performing virtual simulations, enhancing characterization and improving model development
Cost Efficient
Reduces the number of vehicle prototypes required, minimizes instrumentation and data acquisition costs and streamlines final proving ground validation
Enhanced Safety
Expected and unexpected fault conditions more easily detected and safely evaluated in a laboratory environment
Technical Overview
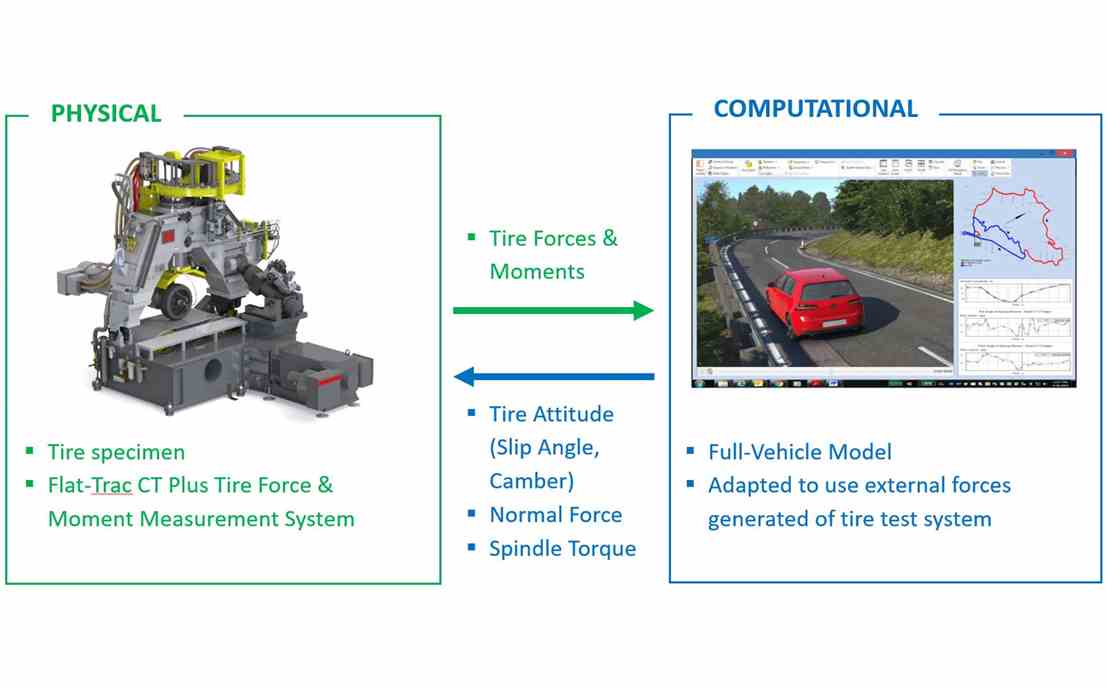
The Iterative mechanical Hardware-in-the-Loop (mHIL) Tire solution allows the combination of physical tires and a virtual vehicle for investigating the interaction between tires and vehicles at the vehicle level. This technique improves over pure computer vehicle simulation by replacing simplified tire models with real physical tires.
- To avoid the need for a specialized four-tire test rig, the hybrid simulation is performed sequentially instead of simultaneously, which requires an iterative technique to achieve the same results as a simultaneous four-tire, real-time hybrid simulation.
- Each corner is simulated independently and the results combined with the vehicle dynamic simulation (which could be real time or not) to create a complete hybrid simulation.
- The model calculates the wheel orientation angles (slip and toe angle), spindle torque and normal tire force. These are incorporated as signals into a drive file, which is then executed once per corner. The tire forces and moments are acquired and used as inputs for the vehicle simulation.
- Only a handful of iterations are typically required to achieve convergence, making this method quick and more efficient than creating a tire model to use with a vehicle simulation.
- A tire test rig with sufficient performance to meet the maneuver requirements is necessary. No special real-time platform or high-speed communication network is required to run the vehicle simulation.
Service and Support
Our experts are here to help keep you up and running.