Hybrid Simulation: mHIL Damper
The mechanical Hardware-in-the-Loop (mHIL) Damper solution combines a computational full-vehicle model with a physical damper test system(s) and damper specimen(s) to create a vehicle-level simulation environment that enables vehicle development engineers to benchmark, characterize, set-up, tune and validate damper systems at the sub-system and vehicle levels.
Applications
Test Specimens
Key Product Features
Accelerated Testing
mHIL techniques compress vehicle development schedules by enabling meaningful evaluation and validation subsystems and vehicles earlier in development - well before the availability of vehicle prototypes
Innovative Technology
Real components can be substituted for difficult-to-model components when performing virtual simulations, enhancing characterization and improving model development
Cost Efficient
Reduces the number of vehicle prototypes required, minimizes instrumentation and data acquisition costs and streamlines final proving ground validation
Enhanced Safety
Expected and unexpected fault conditions more easily detected and safely evaluated in a laboratory environment
Technical Overview
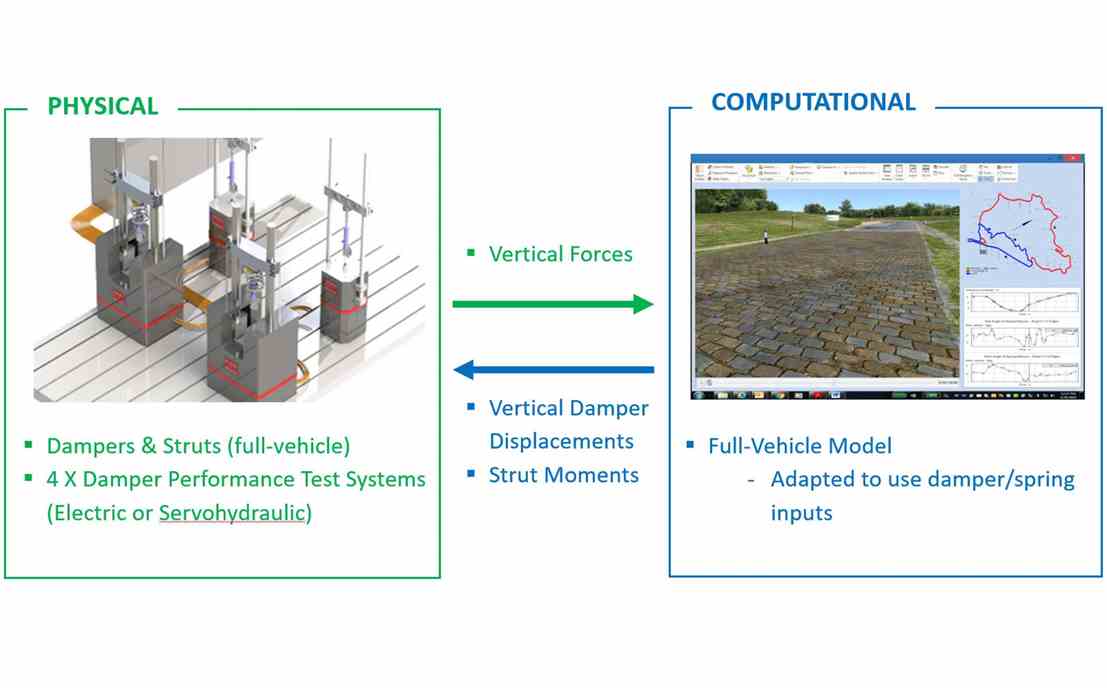
A Mechanical Hardware in the Loop (mHIL) system provides a laboratory method of evaluating the effects of physical chassis elements (in this case the damper sub-system) on vehicle-level attributes (in this case vehicle handling).
- An MTS damper test system or systems with customer dampers installed on it represents the mechanical hardware, which is put in place of modeled damper element(s) within a vehicle simulation model
- The damper sub-system consists of the damper itself including necessary infrastructure and fixturing to simulate a realistic vehicle configuration.
- The damper system can be passive or actively controlled by an ECU.
- The damper system and the ECU are driven in the modeled vehicle on a modeled track as if they were on a real vehicle and track.
The damper test system applies loads and/or displacements to the mechanical damper hardware based on inputs from the vehicle simulation model, measures the hardware response, and then sends these responses back to the vehicle simulation mode. The mechanical hardware is included “in the loop” with the simulated vehicle.
Service and Support
Our experts are here to help keep you up and running.