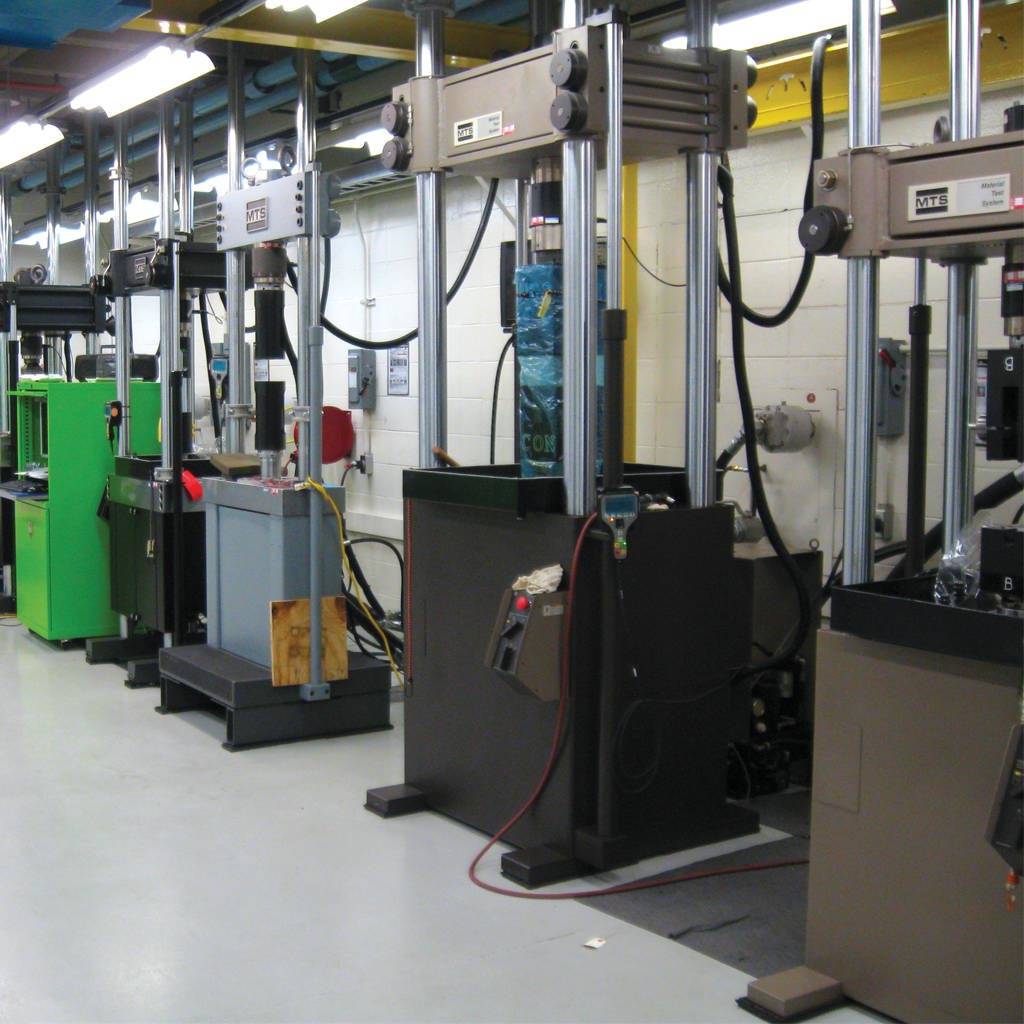
CUSTOMER CHALLENGE
It was a problem that no test program could be expected to handle. Heavy rainfall on June 7, 2008 caused several streams within the White River Basin in southern Indiana to rise to record levels, and major flooding ravaged the area. Along with many homes and businesses, the floodwaters directly impacted the Cummins Inc. headquarters facility in Columbus, Indiana, including its Research and Technology Applied Mechanics Laboratory.
Cummins is a global leader in the design and manufacture of diesel engines and related technologies, offering products that range in size from 3.3L engines to high-horsepower engines up to 78L in size. The Research and Technology Applied Mechanics Laboratory is responsible for ensuring that that all components going into Cummins engines meet exacting mechanical specifications for durability and performance. The lab also develops tests and procedures to support other business units within the company.
For years, this test lab used MTS application software, load frames, control systems, actuators and hydraulic power distribution systems to conduct fatigue evaluations of engine components. The lab team was taking the proper precautions to protect the test equipment with an MTS Assured Maintenance Plan (AMP) that kept the lab current in terms of routine maintenance and calibration, helping to optimize test equipment reliability and test lab uptime.
And then came the flood.
When employees returned to Cummins, they discovered a test lab covered in four feet of muddy creek water. “It was a total loss,” said Lab Manager Paul Gloeckner. “You read about these things in the newspaper, but when you actually walk among the damage, it’s amazing just how destructive water can be. We had load frames, controllers and hydraulic systems that were completely ruined.”
MTS SOLUTION
Even minimal amounts of downtime prove highly disruptive for this busy test lab, so immediate steps had to be taken to restore functionality. “Our MTS service representatives were very responsive from the start,” Gloeckner said. “They helped us quickly sort out what equipment could be refurbished, what needed to be replaced, and the fastest way of getting up and running again.”
Thirteen MTS load frames were refurbished to like-new performance, but a majority of the test lab’s actuators and load cells required replacement. New-generation MTS FlexTest® controllers were installed to run the load frames, along with three new SilentFlo™ hydraulic power units (HPUs) to manage hydraulic power generation and distribution. MTS Multipurpose TestWare® (MPT™) software continued to support the entire test lab.
Alex Duge, Senior Engineer, led the coordination of flood recovery efforts for the test facility. Rather than simply return to the same productivity levels as before the flood, Duge sought to use the disaster as an opportunity to step back, review operations, and identify any potential changes that could enhance efficiency and improve testing capacity going forward.
Prior to the flood, Duge had begun drafting a proposal to update the lab’s antiquated hydraulic systems with new MTS SilentFlo HPUs. He suspected that fluid could be distributed across the test lab with less noise, less heat and lower energy consumption.
“Our MTS support team was familiar enough with our test lab and its layout to provide excellent recommendations for improvement,” Duge said. “Their input was essential for helping us rethink how we’re set up and how we might become more productive.”
CUSTOMER BENEFITS
Once the Cummins Research and Technology Applied Mechanics Lab was back at full operating capacity, the SilentFlo HPUs provided the most obvious operational improvement for the test lab.
“Our older hydraulic systems were very loud and inefficient, and safety was a major concern due to noise, oil leakage, and operating temperatures,” Duge said. “The SilentFlo units have made our lab much quieter and safer, while maintaining our existing flow capacities.
“But the most significant improvement of the SilentFlo units involves the resulting reductions in energy consumption,” Duge added. “Last year, we saved $90,000 on energy costs alone. We’re getting the same hydraulic fluid flow rates from smaller, safer and quieter units that operate at a fraction of the cost.”
Gloeckner attributes his test lab’s longstanding relationship with MTS as a key contributor to the success of his test lab.
“We want to focus on developing better engines, not worrying about test systems and hydraulic equipment, and MTS has allowed us to do just that,” Gloeckner said. “We’ve also learned that whether we’re facing an everyday challenge or a once-in-a-lifetime crisis, we know MTS will be right there alongside us to help us overcome it.”