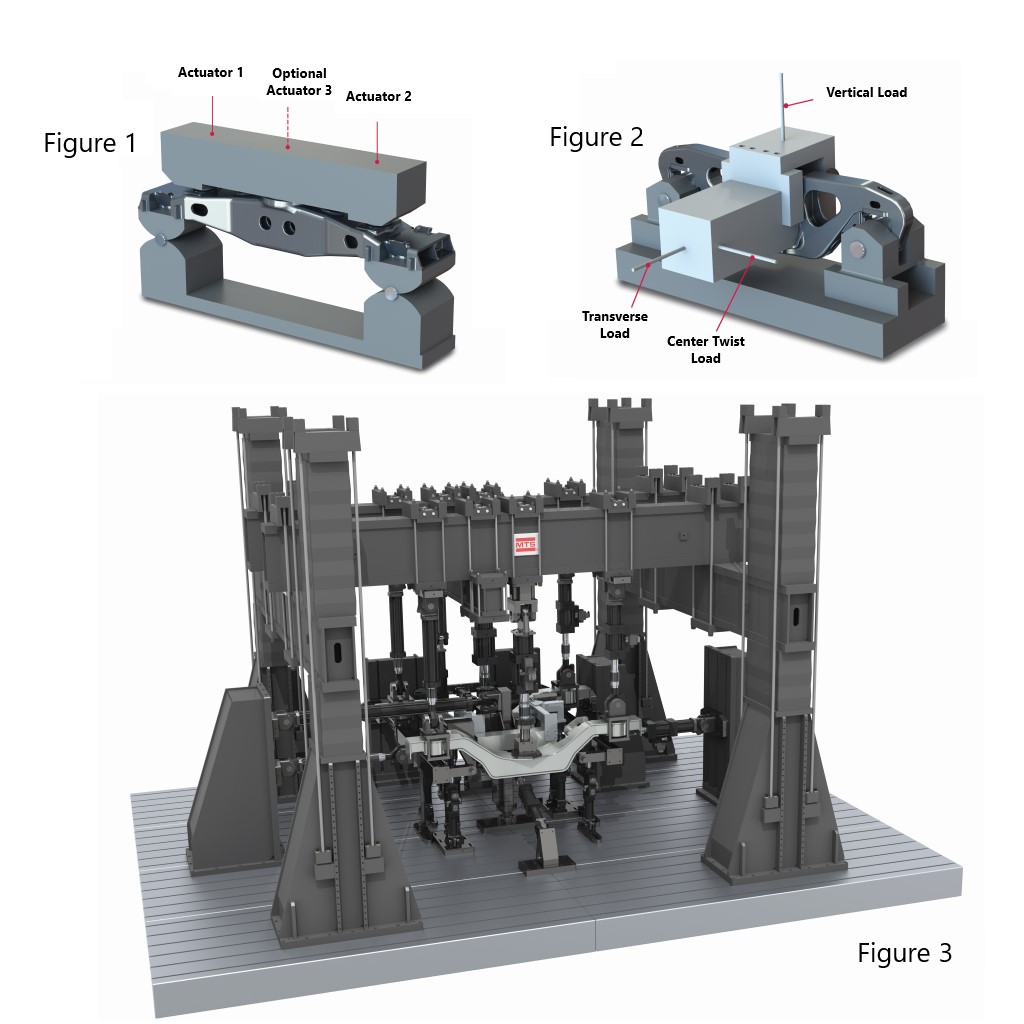
When considering all the components and sub-assemblies that comprise a rolling stock system and its surrounding environment, it helps to draw an imaginary line along the top of the rail. This line divides the system into two major groups. The first group, located above the line, is the “rolling stock,” represented by a bogie frame (or a combination of two side frames and a bolster) along with the primary and secondary suspension and the rail car. The second group, located below the line, is “the way,” represented by the rails, fasteners, sleepers, ballast and other components. The interface between the two groups is the axle with a set of wheels.
While many of the simpler elements in this system can be dealt with through basic component testing, evaluating a component or sub-assembly within the rolling stock requires consideration of three equally important factors: fatigue, performance and comfort.
While fatigue life may not be what the passenger appreciates (or even thinks about) during the ride, it nevertheless represents a very important part in the design and service of rolling stock. Over the course of the last century, the rail industry has come to understand and recognize the importance of fatigue testing in the design and manufacture of rail components. In order to ensure consistent fatigue life and passenger safety, many certification standards have been developed.
MEETING CERTIFICATION STANDARDS
Manufacturers of railway components and subsystems must test components and subsystems to meet the appropriate certification standards, including international standards such as M-202-97 for bolsters, M-203-05 for side frames, and UIC 615 for bogies. These standards help define the tests used to establish the fatigue life and durability of new components, and they are essential for ensuring the safe, long-term operation of passenger, freight and light rail lines.
Bogie, bolster and side frame certification tests require manufacturers to conduct safety and reliability tests on bogie structures and components in specific configurations. Static and dynamic loads are applied in order to evaluate performance, strength and endurance. Test results include yield and ultimate failure load levels as well as fatigue life data.
Three loads are required to test bolsters properly: rock loading, center bounce and edge bounce (see Figure 1). These loads represent the forces the bolster is subjected to in its actual service environment. For the side frame, three loads are required as well: vertical, transverse and center twist (see Figure 2). All of these separate force vectors are important in presenting the proper loads and stress distribution to the specimen and help ensure adequate fatigue life.
For testing bolsters and side frames, an appropriately rated floor-standing load frame is ideal and is relatively simple to fixture. Bogie frame fatigue tests, however, are more sophisticated and complex. The bogie certification tests are defined by international and local standards, and require a higher number of channels and much more complicated fixturing. The loading configurations for the test are based on the configuration of the bogie. The number of axles per bogie, the number of bogies per rail car, and the combined weight of the bogie and rail car are some of the parameters that determine the loads needed for the test. Certification tests require a multi-channel, high-force loading system and typically run millions of cycles. During a test, strain and other signals are collected and analyzed to help designers understand the load dynamics of the service environment, identify areas of high stress and improve designs accordingly. By comparing the strain responses to finite element analysis (FEA) models, engineers can validate the models, which improves future designs.
ADVANCED FATIGUE TESTING
Certification standards are rigorous and involve millions of loading cycles, but they focus exclusively on the minimum set of loads (vertical, transverse and warping) required to verify adequate fatigue life and safety factor. These loads are significantly higher than those expected during normal operation. Loading histories are purposefully conservative to ensure a failure rate as close as possible to zero in all possible combinations of use. This approach has proven adequate for common freight bogies and has been adopted (in some form or another) worldwide.
In modern passenger rolling stock, however, the bogies, suspensions and car interface are much more complex than with freight. High-speed passenger bogies are complex weldments. Items such as dampers, suspension links and auxiliary components (compressors, brake calipers) all present additional loads to the bogie. These loads are often comprised of very different loading vectors and locations than those described by the certification standard. The locations, magnitudes, vectors and phases of these loads are important to consider for test engineers interested in replicating the actual bogie operating environment as realistically as possible.
Complexity quickly becomes an issue in these circumstances. While certification tests typically use fewer than 10 channels (in most cases, fewer than six), more advanced development tests may need more than 20 (and in some cases more than 30) control channels. Combining additional loads with the loads prescribed by the certification standards presents a big challenge in terms of fixturing.
Addressing this complexity is essential. During the past 10 to 15 years, demand has grown considerably among end-users for rolling stock that provides higher reliability, better performance and greater comfort. To meet these needs, manufacturers are developing materials and fabrication methods that were not available when certification standards were first established. New materials – and especially new weight-reduction methods – used in the design and manufacture of practically every component in the railway system have created a need for new development testing procedures that fall outside of the scope of traditional certification testing.
For these larger structural applications, two- or four-column portal frames with custom actuator configurations are required (see Figure 3). Because many of the forces on a bogie are high, the actuators used to replicate these loads are large. Directly applying actuators to load points may require multiple actuators to occupy the same physical space simultaneously. This is a problem that requires substantial expertise in fixturing and kinematic mechanisms to solve. Combinations of actuators, levers, struts (load-bearing columns) and bearings are used to apply the load vectors at the correct locations. Load sensors can be installed on actuators, loading struts and/or reaction fixtures. Swivel bearings on both ends of struts and actuators eliminate side and bending loads. In some cases, the specimen may be inverted to allow better access to loading points.
Cross-coupling – when the action of one actuator affects another– presents serious control issues that must be overcome. The digital controller and software must work together to coordinate the amplitude and phasing of the affected channels to remove the risk of interference and ensure accurate loading. Typically, advanced control techniques are involved. The entire system, including the specimen, frame and actuator subsystem, might contain some natural nonlinearities. Accounting for these nonlinearities may require modification of the drive signals to achieve the desired loading history on the specimen.
Adjustments are typically made with advanced signal processing software, such as MTS Remote Parameter Control (RPC®), which is based on the frequency response function (FRF) matrix of the entire system. The software measures the controller command and compares it to the amplitude and phase of the specimen responses across the desired frequency range. A cross-coupling matrix is generated that includes all cross-coupling and other linear differences between command and response. This FRF is then inverted and multiplied by the desired response. The result is an actuator drive file that compensates for cross-coupling and related issues. Nonlinear contributions are corrected by calculating the error, creating a corresponding correction file, and then applying the correction to the previous drive file. This iterative process is repeated until the desired accuracy is achieved. Applying such control compensation techniques allows the test to run accurately at a much higher frequency, which reduces test time and increases test quality.
While this is taking place, engineers must be able to collect and manage large amounts of data. The test system may need to accommodate, for example, up to 250 strain gage and displacement channels to find potential vulnerabilities in the design. Some of this data needs to be collected in real-time for use in the control system, while even larger amounts of data need to be collected for offline analysis and comparison with computer-aided engineering (CAE) models.
Overcoming all of these challenges is difficult, but worth the investment. The results enable component manufacturers to optimize designs, differentiate new product offerings, and provide the confidence customers need in the quality and reliability of new components.
