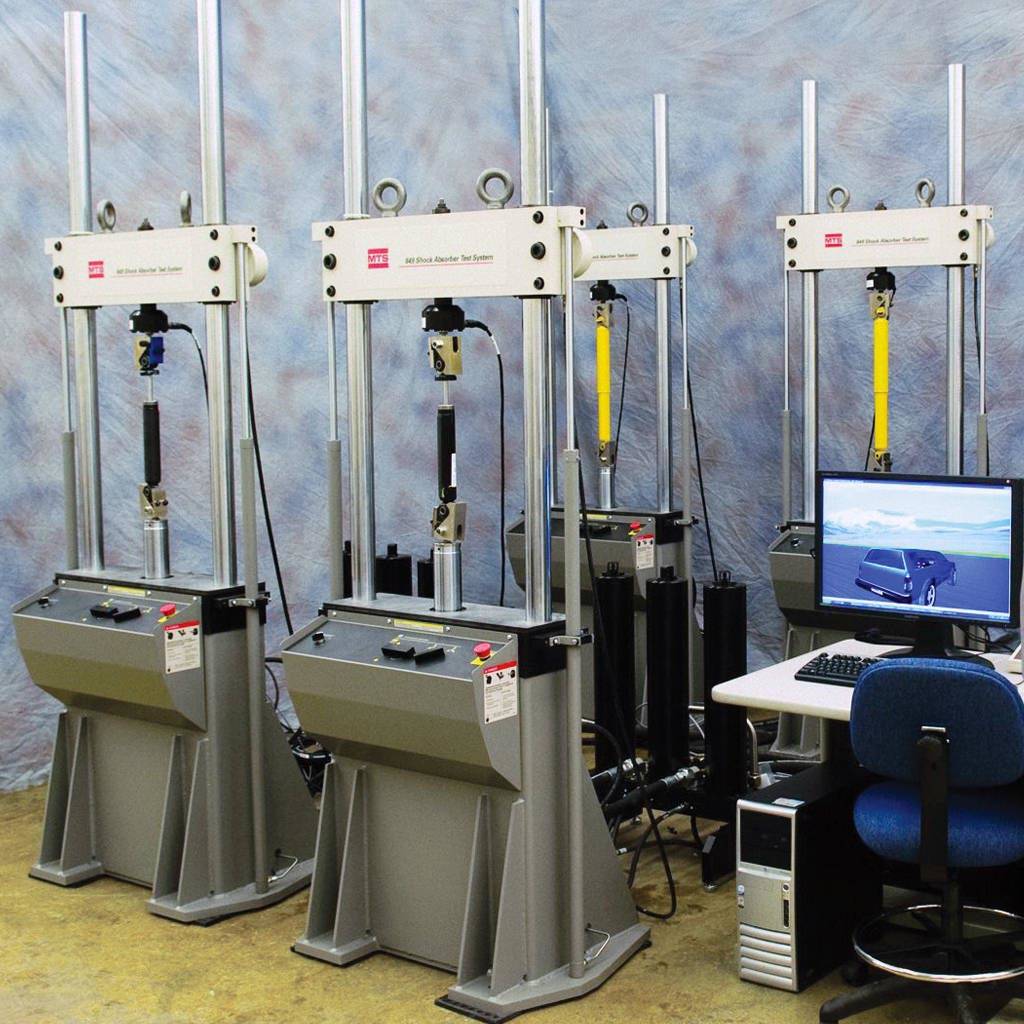
DÉFI DU CLIENT
Nissan® met tout en œuvre pour répondre à la demande des consommateurs qui recherchent des produits de haute qualité et de haute performance. Pour répondre à ces demandes dans des délais raisonnables, il faut non seulement que le développement soit efficace, mais que la validation le soit également afin d’éviter les itérations longues et coûteuses entre les deux activités. L’amélioration continue des outils et des méthodes est particulièrement importante lorsqu’il s’agit d’atteindre les objectifs en matière de dynamique des véhicules, où les ingénieurs cherchent constamment à obtenir une vision plus approfondie sur les performances des sous-systèmes utilisés dans les véhicules à un stade précoce du développement.
Bien que les outils d’ingénierie assistée par ordinateur (IAO) soient en mesure de prédire les performances en temps opportun, ce qui permet de réduire le temps et les coûts de développement, certaines limites empêchent ces outils de révéler des phénomènes inattendus ou inconnus pendant le développement. Le fait de ne découvrir ces phénomènes qu’au moment d’être sur la piste comporte des risques en termes de budgets et de calendriers. Pour éviter les risques liés à une découverte tardive, il est possible d’effectuer des essais physiques pendant le développement, en plus de l’IAO. Cela devrait permettre d’améliorer l’évaluation des performances et de réduire le besoin global de prototypes, ce qui entraînera une réduction des coûts.
Les ingénieurs automobiles de Nissan Motor Co., Ltd. souhaitaient pouvoir passer de la conception définitive au démarrage de la production en l’espace d’une année civile. Pour atteindre cet objectif, les atouts complémentaires de l’IAO et des procédures d’essai devaient être renforcés, notamment en comprenant parfaitement comment les sous-systèmes du véhicule fonctionneront et agiront sur les performances des uns et des autres. Afin de respecter des délais de développement aussi serrés, il fallait obtenir ces informations bien avant que le prototype du véhicule ne soit disponible.
A l’époque, l’entreprise était en train de mettre au point un nouveau système d’amortisseurs et prévoyait d’étudier les possibilités de tester ce sous-système avec plus de précision et à un stade plus précoce du développement. Après une brève phase de recherches, Nissan a décidé de s’associer à MTS, en raison notamment des 40 ans de leadership mondial de l’entreprise dans la technologie et l’expertise des essais de véhicules.
SOLUTIONS MTS
MTS a travaillé en étroite collaboration avec Nissan pour déployer la technologie Mechanical Hardware-in-the-loop™ (mHIL), qui permet d’évaluer les performances du véhicule avant que le prototype du véhicule complet ne soit disponible.
La technologie mHIL de MTS vient compléter la technologie Hardware-in-the-loop (HIL), qui est largement utilisée pour valider les unités de commande électronique (ECU), en plaçant des systèmes ou des composants mécaniques dans la boucle d’un modèle de véhicule en temps réel. Etant donné que la technologie mHIL utilise de vraies pièces, elle est plus sensible que l’IAO seule, ce qui se traduit par des décisions de développement plus efficaces. En outre, la technologie mHIL donne aux ingénieurs la possibilité de faire fonctionner ces pièces dans un environnement virtuel qui permet de résoudre et d’éviter les problèmes à un stade beaucoup plus précoce du développement des véhicules. Les prototypes sont ainsi plus robustes et, en fin de compte, la validation et le travail sur piste sont plus efficaces.
MTS et Nissan ont lancé un programme pilote utilisant la technologie mHIL pour valider les performances des nouveaux systèmes d’amortisseurs en cours de développement chez Nissan. Ce système d’essais pilote est finalement devenu le système d’essais des amortisseurs à quatre postes de MTS, qui est actuellement utilisé par les ingénieurs de Nissan. Les résultats du programme pilote ont montré une meilleure corrélation entre les données d’essai et les essais réels sur piste en ce qui concerne l’analyse du confort de conduite et de la maniabilité. Grâce au système d’essais des amortisseurs à quatre postes de MTS, Nissan a pu réduire de 40 % les modifications rétroactives apportées à ses véhicules en cours de développement.
AVANTAGES CLIENTS
En associant le système d’essais des amortisseurs à quatre postes de MTS à la technologie mHIL, Nissan a pu identifier et résoudre les problèmes liés aux comportements inattendus des sous-systèmes à un stade précoce du développement des véhicules. Cette technologie représente pour Nissan un gain de temps et d’argent considérable, car elle met en évidence des phénomènes inattendus qui n’apparaissaient, auparavant, que lorsqu’un prototype était testé sur une piste d’essai.
« La technologie mHIL de MTS nous permet de découvrir et de résoudre les éléments inconnus du déploiement de la fonction qualité pendant la phase de préparation, ce qui réduit d’au moins un mois le temps d’essai de nos véhicules », a déclaré Yoichi Sakai, responsable du développement expérimental des systèmes chez Nissan. « A une époque où de nombreux constructeurs réduisent le développement expérimental de leurs véhicules, la technologie mHIL nous offre une solution rapide, précise et abordable pour poursuivre ces initiatives. »
« De plus, grâce à l’efficacité obtenue par la technologie mHIL, nous pouvons également proposer aux consommateurs des véhicules de meilleure qualité à un prix plus abordable », a ajouté M. Sakai.
En 2008, MTS et Nissan Motor Co., Ltd. ont reçu le prix de l’outil de développement de l’année du magazine Vehicle Dynamics International, pour leur collaboration dans le développement du système d’amortissements à quatre postes doté de la technologie mHIL.
« La technologie mHIL représente une véritable révolution en matière de rapidité et de rentabilité du développement des véhicules », a déclaré M. Sakai. « Elle a été extrêmement bénéfique pour Nissan, et elle le sera certainement tout autant pour les fournisseurs. »